- Home
- News
- Controlling Particulate Contamination with Fabric Curtain Walls
Controlling Particulate Contamination with Fabric Curtain Walls
Controlling Particulate Contamination with Fabric Curtain Walls
by Chuck Ashelin
Contamination control is critical in a wide spectrum of industries, none more so than food manufacturing and processing. From the mixing and packaging of powdered ingredients and spices to grain storage and loading dock operations, control is vitally important to a myriad of food industry processes.
At the very least, particulate matter in the air is a nuisance. However, it can cause serious quality and safety issues as well. At the nuisance level, particulate generated from cutting, grinding, mixing, etc., can settle on surfaces significant distances from the operation if containment equipment is not in place. Dust on neighboring equipment, furniture, office equipment, windows, and floors becomes a constant drain on cleaning and maintenance resources. On the more serious end of product quality, uncontrolled particulate matter can spoil or degrade batches of differing critical materials, particularly in food processing.
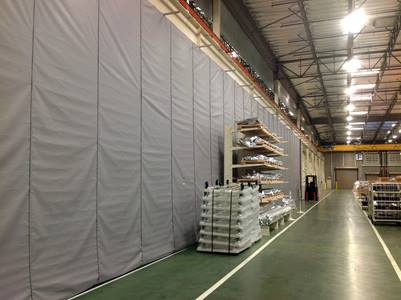
From a safety standpoint, there are many circumstances where high enough concentrations of airborne dust-sized particulate in a closed space can become explosive or flammable. This includes seemingly innocuous products we wouldn't normally think of as explosion hazards - including grain, flour, sugar, and powdered milk. Additionally, airborne particulate can be a health threat to employees. These risks can range from a skin, eye, or bronchial irritation to more serious issues for people with asthma. Most serious can be the potential for particulates to cause lung diseases like cancer.
Controlling Particulate Contamination
Several methods can be used to keep particulate in one space from contaminating another, including:
- Local exhaust – a high-velocity airflow stream captures particles at the point they are generated and carries them away;
- Exhaust with filtration – a high-velocity airflow stream captures particles and recirculates them through a filter medium, where they are removed;
- Area exhaust – a high-volume exhaust fan draws air from the full room volume to an outside vent or recirculates through a filtration/separation device; and
- Barrier separation – simply a wall or partition between affected areas. These are especially effective when used to separate clean from ambient spaces in a positive or negative air pressure environment, such as between a loading dock and a food processing area, or between food processing or packaging lines and surrounding areas.
Exhaust separation methods rely on moving a volume of air containing the contaminate particles. Barrier separation can be enhanced by creating a positive or negative pressure differential across the barrier. Each of these could be accomplished through the use of exhaust fans through ducts to create a negative air pressure environment. A local exhaust setup would incorporate some type of hood designed to collect the air and particulate being moved and funnel it into the exhaust ductwork. Area exhaust would include multiple draw points through louvered openings in the ceiling or wall. Either of these methods could, and most likely would, include some type of filtration or particle separator in line to remove particulate from the air stream. This is necessary prior to either recirculation of the air back into the space, or discharge of the air into the atmosphere.
Conversely, in a clean space where offending particulate is not generated, but adjacent space contains foreign matter that could contaminate product in the clean space (e.g. food processing or packaging), a positive air pressure environment would be desired. In this case, filtered air would be pumped into the clean space, creating a positive air pressure within the space and preventing inwardly flowing air currents that could carry foreign particulate matter.
In some cases, a simple partition (wall) between a clean space and an uncontrolled ambient space (such as between a processing area and a loading dock) is an effective means of separation. If negative air pressure differential exists across the wall between the clean and ambient space, the wall acts as a physical barrier, blocking most of any potentially contaminating foreign matter from crossing the barrier. Depending on the degree of particle separation required, and the need and frequency for traffic to move through the partition, a more effective solution would be to introduce a positive air pressure differential to the clean space, as described in the paragraph above.
Fabric Curtain Walls Can Help
Curtain walls can significantly improve the effectiveness of these systems, as well as offer the opportunity for cost savings, both in the initial cost of the equipment and in the direct operating cost.
Anytime a space is to be exhausted, the smaller the space can be made, the smaller the exhaust equipment can be specified. Partitioning around a dust source with a fabric curtain wall takes full advantage of this relationship. By reducing the volume of the space to be exhausted, smaller fan(s) can be used, reducing the total air movement. Lower air velocity through filter media increases the effective particle separation of the device. Additionally, lower airflow through the filter reduces the frequency required for change out or cleaning.
In a situation where a positive pressure space is desired, some sort of enclosure, or “box,” around the space would be optimal to maintain the pressure differential. Fabric curtain walls are an ideal partition solution. They are less expensive to install than hard walls and create an enclosure seal just as effective as a hard wall (in some cases more so, if there are many penetrations through the partition like piping, conduit, etc.).
Separation between a loading dock area and a desired clean space in a packaging or processing facility is a common issue. In many cases, leased or previously purposed buildings make no provision for this kind of separation. Production efficiency mitigates toward minimizing product transfer distances and times between production and shipping or receiving areas. With dock doors often open, and truck traffic traveling into and away from the dock, a negative air pressure condition in the building can readily draw airborne contaminants into the building and clean space.
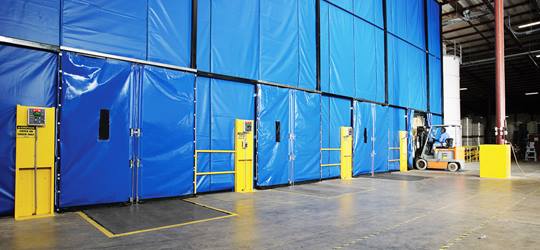
The addition of a fabric curtain wall in this application creates an effective barrier between the uncontrolled environment of the dock area and any clean area. The inclusion of standalone, high-speed, roll-up doors in the curtain wall allows for efficient thoroughfare, while minimizing time the interior is open to the loading dock area. Infiltration could be further reduced by positively pressurizing the interior clean space.
As described above, in addition to reducing the volume of space to be exhausted or supplied, fabric curtain walls act as a very effective physical barrier on their own, blocking transfer of particles from space to space. Curtain walls can be single-layer fabric or multi-layer insulated. They can easily be fitted with clear vision panels for visual communication between spaces.
Curtain walls are flexible by nature, yet very durable. They can withstand contact from machinery or product, and simply “bend without breaking,” in contrast to a hard permanent wall. They are also relatively easy to reconfigure if a space needs to be enlarged, reduced, or the shape of the space footprint needs to change. No “deconstruction” is required. Fabric curtain walls are easily installed, can be simply trimmed around conduit, piping, ductwork, etc., and can be anchored to the floor to withstand pressure differential across them.
Depending on the application, a curtain wall can be suspended from the room ceiling or can be supplied with a standalone framework to hang from. They are available as stationary as well as sliding (suspended from roller track), and can be fitted with strip curtains, personnel doors, or high-speed industrial doors for full range of access to the space.
Curtain walls can be an ideal choice for facilities looking to control particulate contamination. As a flexible and economical way to partition space, they make exhaust, supply, and separation systems for dust more efficient—regardless of the application.
Ashelin is engineering manager for Zoneworks. A 15-year industry veteran, he holds a bachelor’s degree in chemical engineering. Reach him at cashelin@ritehite.com.
AUTHOR DISCLAIMER: The information herein is provided as a general reference regarding the use of the applicable product(s) in specific applications. This information is provided without warranty. It is your responsibility to ensure that you are using all mentioned products properly in your specific application and in accordance with all laws and regulations.
Back to News