- Home
- News
- Is Your Loading Dock OSHA Compliant?
Is Your Loading Dock OSHA Compliant?
Industrial safety regulations encompass a broad spectrum, with OSHA at the forefront of setting and enforcing these standards. OSHA, which stands for the Occupational Safety and Health Administration, plays a pivotal role in ensuring safe and healthful working conditions for employees. With its mission centered around workplace safety, OSHA compliance becomes essential to all dock operations. Whether leasing or designing a new facility, entering a career as a safety professional or running a facility’s operations, it's important to have a finger on the pulse of evolving safety standards.
We’ve put together a loading dock safety checklist to help:
Instituted in 1978, this standard requires facilities to secure trucks or trailers at the loading dock. The goal is to help ensure trucks remain stationary and flush to the building during loading and unloading operations. Supported by the increased reporting and recognition of trailer separation accidents at the dock, primarily early departure, the standard first only denoted wheel chocks as an applicable means for securing trailers. However, one year after the introduction of the original Dok-Lok® in 1980, the language was amended to include “mechanical means” as a preferred alternative to wheel chocks.
Vehicle restraints have expanded beyond the original RIG-based restraint to include Rotating Hook Restraints, Stabilizing Trailer Restraints, Vertical Barrier Restraints and Wheel-Based Restraints.
Taking safety a step further in helping prevent trailer separation accidents, active restraint status inside and out is critical. Communicating to material handlers when it’s safe to enter and trailer and truck drivers when they can safely depart, light communication has been standard with all Dok-Lok vehicle restraints since 1980. In recent years, restraint status has been extended to the upper corners and to the sides of the leveler in the case of stacked pallets blocking controls. So now, material handlers can have line-of-sight restraint status to immediately know which docks are actively loading.
For ultimate safety, multiple pieces of loading dock equipment including vehicle restraints can be programmed into an interlocked sequence of operations. Protecting both equipment and pedestrians, interlocking optimizes a facility's standard operating procedures by effectively removing human error from the equation. Safe sequence of operations enhances safety and productivity with the simple push of a button.
Slips, trips and falls are cited as the second-most common workplace incident by OSHA. In fact, slips, trips, and falls cause
nearly 700 workplace fatalities per year which is 15% of all workplace deaths. One often overlooked area of the facility with an opportunity for drastic falls is the loading dock. With most loading docks having a 4’ drop off, this OSHA standard helps protect equipment, products and people. Some loading dock safety barriers meet the “Walking, Working Surfaces” guardrail requirements. However, not all safety barriers are made equal. The Dok-Guardian® XL safety barrier is designed to meet the standards by stopping impacts up to 30,000 lbs. with a 58” tall manually retractable curtain without compromise. For facilities with smaller loads, a light-duty model offers a cost-effective solution that stops up to 5,500 lbs. For improved employee comfort, powered dock gates have push button operation, which helps minimize strain on workers. These safety barriers can be interlocked with a vehicle restraint to ensure it’s not retracted until the trailer is safely restrained at the dock, further addressing trailer separation accidents.
Loading dock levelers can be equipped with a safety barrier lip which also helps prevent a forklift from running off the edge of dock. However, this does not satisfy the requirement so it should be paired with a Dok-Guardian XL. With a dock door being no match to a forklift, these paired solutions provide additional layers of pedestrian and forklift protection in both open- and closed-door applications.
Recently introduced, this requirement emphasizes the significance of ergonomics and a smooth transition. Given recent labor shortages paired with an aging workforce, this standard is designed to promote employee comfort and safe operation of loading dock equipment.
Oftentimes a literal sore subject for material handlers, loading dock levelers are needed to bridge the gap but have historically emphasized function over comfort in their design. Crossed over on average 100,000 times per year, the repetitive trauma is bad for the bottomline. So much so that a study published by a researcher at The Ohio State University reports that severe back injuries that occur when a person is hurt over and over again can cost as much as $300,000. However, in 2005, Rite-Hite revolutionized the industry with the introduction of their hydraulic loading dock levelers engineered with smooth transition at the forefront. Offering significant ergonomic and productive benefits over mechanical leveler options, the hydraulic levelers meet the OSHA requirements while reducing whole body vibrations at the dock - commonly referred to as “dock shock”. Ergonomics at the loading dock are further enhanced with well-maintained modernized forklifts, stabilizing trailer restraints, trailer lifts and stabilizing trailer stands. This comprehensive system has been tested to improve relative smoothness of transition from leveler to trailer bed by ≥ 120%.
Consult Rite-Hite for a Loading Dock Safety Assessment
OSHA plays an undeniable role in workplace safety, so understanding these requirements and compliant loading dock solutions will lead to increased safety and productivity. Rite-Hite's comprehensive offering of solutions, spanning a wide variety of budget and application, simplify the important task of staying compliant and on top of safety regulations and safety trends for safety managers, architects and more.
At Rite-Hite, we are committed to being a strong, experienced partner when it comes to your loading dock safety needs. So much so, that our local representatives are trained to come to your facility and perform a customized, no risk safety assessment to perform inspections, analyze and make recommendations specific to your loading dock safety needs.
Schedule a Loading Dock Safety Assessment
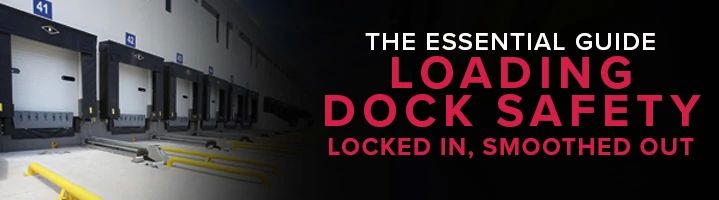