- Home
- News
- cGMP Requirements and Common Violations
cGMP Requirements and Common Violations | Rite-Hite North America
Current Good Manufacturing Practices, or cGMP, are regulations for manufacturers that are enforced by the FDA to protect consumers. The cGMP requirements cover the manufacturing processes for a variety of industries, including pharmaceuticals, food and beverage, dietary supplements, cosmetics and medical devices.
To ensure that risk to the end-consumer is as low as possible, the cGMP regulations strive to have manufacturers consistently release a product that is free from contamination, consistent in quality and documented throughout the manufacturing process by approved personnel.
These cGMP facility requirements, while important and well intentioned, have been troublesome to many manufacturers. To that point, penalties for cGMP violations are not to be taken lightly since penalties can vary drastically from product recalls and seizures to criminal penalties that can include hefty fines and, in some cases, jail time.
The good news is that, over time, we’ve been able to identify trends in common cGMP violations that should be reviewed and compared to what your existing facility operations. First, we will take a look at what cGMP regulations mean, followed by common violations and how embracing new technology can protect your company from the pitfalls of these infractions.
What cGMP Regulations Mean for Manufacturers and Shippers
The specific requirements to be met can be found under the Code of Federal Regulations (CFR), Title 21. We will be providing a general overview of requirements for the pharmaceutical and food and beverage industries, but your company will need to be vigilant in its operational procedures to comply with the details for its particular industry and processes.
cGMP Regulations for Pharmaceuticals
21 CFR Parts 210 and 211
According to the FDA, these regulations contain the minimum cGMP for “methods to be used in, and the facilities or controls to be used for, the manufacture, processing, packing, or holding of a drug to assure that such drug meets the requirements of the act as to safety, and has the identity and strength and meets the quality and purity characteristics that it purports or is represented to possess.”
This is a lot to unpack, but Part 211 breaks down these requirements into sections of the manufacturing process, as well as facility requirements:
- Organization and Personnel - requirements for personnel qualifications and responsibilities, consultants and responsibilities of quality control units
- Buildings and Facilities - design, lighting, ventilation, air filtration, air heating/cooling, sanitation and maintenance
- Equipment- design, size, location, construction, maintenance, filters and specifics for automatics, mechanical and electronic equipment
- Control of Components and Drug Product Containers and Closures - testing and approval, containers, closures, storage and rejected components
- Production and Process Controls - written procedures and deviations, sampling and testing of in-process materials and drug products, control of contamination and reprocessing
- Packaging and Labeling Control - materials examination and usage criteria, packaging and labeling operations, drug product inspection and expiration dating
- Holding and Distribution - warehousing and distribution procedures
- Laboratory Controls- includes various requirements for testing, sampling and distribution
- Records and Reports - complaint files, distribution and laboratory records, both production and control records, master production and control records, equipment cleaning and use log and component, drug product container, closure and labelling records
- Returned and Salvaged Drug Products
cGMP Requirements for Food and Beverage
21 CFR Parts 110, 111, 117
Part 110 is known as the cGMP in Manufacturing, Packing or Holding Human Food. It is, in many ways, similar to the regulations for pharmaceuticals. The regulations cover personnel, buildings and facilities, equipment, production and process controls and defect action levels.
Part 111 is specific to dietary supplements, but it goes into much further detail for what is important for adherence to cGMP requirements - having an approved Production and Process Control System that includes several sections, including:
- Establishing a Production and Process Control System
- Requirements for Quality Control
- Requirements for Components, Packaging and Labels
- Requirements for the Master Manufacturing Record
- Requirements for the Batch Production Record
- Requirements for Laboratory Operations
- Requirements for Manufacturing Operations
- Requirements for Packaging and Labeling Operations
Part 117, however, is specific to Hazard Analysis and Risk-Based Preventive Controls, which beyond record keeping, preventative controls and facility exemptions, also focuses heavily on your facility Supply-Chain Program that details:
- General Requirements Applicable to a Supply-Chain Program
- Responsibilities of the Receiving Facility
- Using Approved Suppliers
- Determining Appropriate Supplier Verification Activities
- Onsite Audits
- Records Documenting the Supply-Chain Program
Trending and Common cGMP Violations
All of these cGMP requirements are important for the safety of personnel and the end-consumer, but there are specific aspects of the guidelines that companies will often falter in its compliance: Production and Quality Control.
You may have thought your historical production or QC operations were sufficient, but under cGMP guidelines, this isn’t always the case.
A common problem occurs when a facility doesn’t adjust its production and quality control practices for cGMP compliance. Since its old methods may not align with current guidelines, many companies have issues with inspectors looking for the specific cGMP demands, resulting in violations.
Diligent adherence to all the details of the cGMP is necessary to avoid many of the common cGMP violations that include:
Current Good Manufacturing Processes for Production
- Equipment and facilities aren’t properly designed or maintained to meet construction or sanitation requirements
- Pharmaceutical contamination from lack of oversight to follow the mandated operational checkpoints or by non-approved personnel
- Production and process controls don’t follow the mandated guidelines, which can invalidate all records that don’t adhere
- Plant and Grounds violations that allow or have the potential to harbor pests
Current Good Manufacturing Processes for Quality Control
- Defects and complaints don’t meet guidelines to determine either cause or impact
- For pharmaceuticals, having products that differ in strength, purity or quality being released
- Not following testing or inspection requirements or not documenting testing properly, which can lead to an inconsistent product
- Failure to establish and follow written procedures for QC operations
- Lack of an accurate temperature monitoring/reporting device in each freezer or cold storage compartment, leading to potential for decay, mold growth or cross-contamination.
Technological Solutions for cGMP Regulations
GMP isn’t anything new, but since rebranding as cGMP, the goal was to make it clear that manufacturers need to be current in their practices, while still allowing for flexibility in how to comply. Maintaining compliance and staying current oftentimes means staying up-to-date by implementing new technologies, like Door-Commander advanced controls.
The Door-Commander™ from Rite-Hite, for instance, is an interactive operating system that uses low-voltage connections to provide access to door settings without requiring workers to access high-voltage control panels when providing maintenance or troubleshooting. In addition, realtime and historical data is available that can be integrated with your current building management systems.
This addresses aspects of cGMP requirements in the areas of safety, maintenance and record keeping, all in one efficient package.
On a related note, beyond Door-Commander integration, your industrial doors are a great example of an area where technological advances can address cGMP safety, cleanliness and maintenance regulations. Rite-Hite’s pharmaceutical clean room doors, for example, are designed to address common contamination hazards like chemicals and bacteria.
Specifically, the FasTrax Wash Down Door is designed to comply with USDA, FDA and cGMP standards for clean-up. It’s one-piece radial header is machined from a block of UHMW plastic in addition to its polypropylene door fabric that boasts a higher resistance to acids and bases than standard vinyl or urethane. In addition, the FasTrax Clean includes wash down-friendly, non-corrosive side frames that are optimal for bacteria control.
Similarly, the SplitSecond Pharmaceutical Clean Room door incorporates contemporary high speed door performance while complying with various regulations through use of corrosion resistant materials and including three sets of reversing thru-beam photo eyes, making it an industry leader in safety for high speed doors.
At the end of the day, cGMP requirements are not a suggestion. While flexible, these are the rule of law and there is no option but to comply. It may seem tedious, but it’s really for the good of your personnel and for the consumer that is using the products your facility manufactures.
Knowing and adhering to these requirements by use of new technologies may not be quick and easy, but it’s imperative. We hope that disclosing these common cGMP violations will allow your facility operations to take a closer look at your procedures to ensure you produce a quality product that is properly documented and safe for everyone involved - from manufacturing to the end-user.
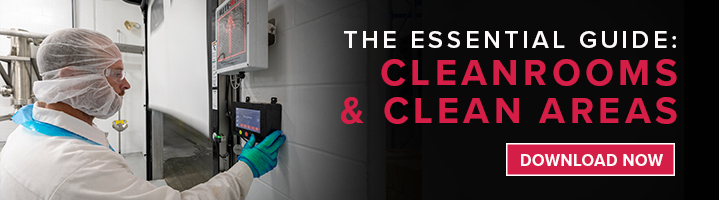