- Home
- News
- Going Vertical: Fall Prevention a Key for Taller Cold Storage Facilities
Going Vertical: Fall Prevention a Key for Taller Cold Storage Facilities
Cold storage warehouses, it seems, are like NBA point guards – they just keep getting taller. When employees have to climb and reach for more products, the odds also increase for slip and falls.
Driven by the boom in online shopping, faster delivery expectations and changes in consumer tastes – including a preference for fresh and organic foods versus shelf-stable fare – more warehouses are being built in urban areas with a high population density. To compensate for the increased price of land, many companies have decided to “go vertical” and build upward, rather than outward.
Cost of Refrigerated Warehouse Construction and Maintenance
The relatively high cost of operating a cold storage warehouse (as much as 3 times that of standard warehouse) has also made this sector receptive to taller building designs.
Of course, basic physics plays a role. Since heat infiltration is greatest through the floor and roof, taller buildings have better energy efficiency than lower or wider buildings of equivalent volume.
Automated Solutions that Put Workers at Slip and Fall Risks
Advances in automation have been a key component in making these facilities operationally viable. Automated guided vehicles (AGVs) are regularly used to improve throughput speed of products from end-of-line equipment to shipping, for example, while automated storage/retrieval systems (AS/RS) reach product at various levels without putting the human workforce in dangerous situations.
Fall Prevention Strategies for Cold Storage Warehouses
The trend toward taller cold storage facilities has also made fall protection equipment critical . Industrial mezzanines must have handrails and gates around all edges. However, these gates need to be opened to accommodate the loading and unloading process. According to ANSI, companies must provide full-time protection when loading and unloading materials from an elevated platform; there can be no exposed areas where an employee could potentially fall.
Dual reciprocating barriers, such as Rite-Hite’s GateKeeper, are a common choice for mezzanine applications, since they create a controlled access area in which the inner gate and outer gate cannot be opened at the same time. The GateKeeper uses a link bar design that ensures both gates work in unison; when the outer gate opens to allow pallets in, the inner gate automatically closes to keep workers out. A safety latch that can only be accessed when standing outside the work zone prevents the outer gate from being raised by a worker inside the work area.
Many facilities are also using multi-level pick modules to handle order fulfillment. Pick modules are typically constructed using a metal support structure, flooring, stairways, handrails, and landings. Products are stored in shelving and racks and are “picked” to conveyors, totes, carts, and other transportation systems.
These multi-level rack systems pose a number of challenges when it comes to securing open areas during loading and unloading. The work areas are typically very small and are contained within the rack system itself, which makes it difficult to integrate traditional safety barrier designs.
While they function similarly to reciprocating mezzanine barriers (inside gate can’t open when the outside gate is, and vice versa), rack barriers utilize the existing rack structure to minimize the footprint in existing or new installation rack bays. Leading models, such as Rite-Hite’s RacKeeper, can fit within virtually any type of rack configuration and meet applicable OSHA standards, as well as other types of regulations.
Regardless of the specific fall protection equipment needed, facilities preparing to “go vertical,” need to have a solid foundation of safety equipment in place. Learn more by downloading the "Essential Guide to Cold Storage."
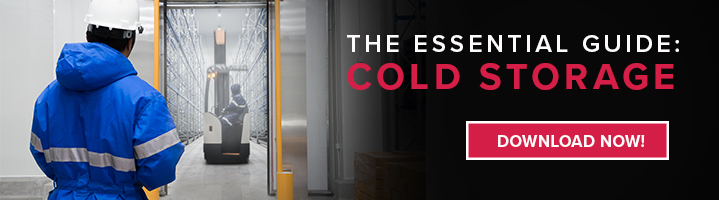