- Home
- News
- 3 Challenges Facing Cleanrooms
3 Challenges Facing Cleanrooms
Facilities managing cleanrooms face a host of challenges. In these critical environments, the risks are amplified if left uncontrolled. That’s why it’s essential for facility managers to understand current regulations, be aware of contamination risks, and balance costs.
Regulatory Compliance over Cleanroom Environments
The most basic challenge for any clean area environment is meeting regulatory standards.
Between evolving best practices, new technology and regulatory updates, it’s a never-ending job to remain in compliance. Here are the main regulations that facility managers should be familiar with:
- International Organization for Standardization (ISO) sets universally recognized guidelines. Specifically, facility managers should know ISO 14644, which defines the allowable levels of particulate matter in clean rooms categorizing them from 1 (cleanest) to 9 (dirtiest).
- To control cleanroom design, sections of the Current Good Manufacturing Practice (cGMP) guidelines particularly lay out the use of anti-microbial doors and walls that can be treated repeatedly with harsh chemical cleaning agents.
- Hazard Analysis and Risk-based Preventive Controls for Human Food of the Current Good Manufacturing Practice also includes:
- 21 CFR Part 117 regulates the development and maintenance of cleanrooms and clean areas in food processing facilities.
- 21 CFR Part 820 (cGMP) Subpart G regulates the production and process controls of cleanrooms.
Cleanroom Environments and Listeria
Listeria is a top bacterial concern for most food facilities, particularly in the Ready-To-Eat (RTE) sector, which relies on aseptic processing. Although this advanced sterilization process has been generally positive for both the industry and consumers, there is a negative trade-off: increased listeria concerns.
According to many industry researchers, some organisms in non-aseptic facilities were actually beneficial. Today, the aseptic process leaves no inhibitors for listeria. That’s why there is discussion about spraying down walls, doors, floors and equipment with competitive bacteria that would only combat the contamination.
While there hasn’t been any true acceptance by the FDA or USDA about this, facility managers need to stay updated on best practices for controlling listeria.
The High Cost of Cleanrooms and the Consequences of Design Overkill
In all industries, the costs of implementing cleanrooms and clean areas are a big challenge.
In pharmaceutical, for instance, construction costs for an ISO 7 to ISO 8 cleanroom can range from $250 per square foot to $1,500 per square foot, largely due to the use of stainless steel for corrosion resistance. That’s why many facility managers are turning to modular construction to reduce cost and build time.
“Design overkill” may also contribute to cost problems, particularly in electronics manufacturing. Ranging from $180 to $2,800 per square foot, electronics industry clean rooms are typically designed and constructed in tight time periods. Engineers may opt to duplicate past cleanroom designs to meet deadlines and avoid the potential risks arising from new layouts. In some cases, however, that approach can lead to cleanrooms that exceed the process needs of the facility – a waste of valuable resources.
Find Safe Solutions for Cleanrooms and Clean Areas
By gaining an in-depth understanding of the challenges facing clean rooms, facility managers can implement solutions. Employee training, cleanroom equipment, and customized planning can help facilities better follow current regulations, reduce contamination risks, and maximize investments.
This blog was developed from the Essential Guide: Cleanrooms and Clean Areas. For additional information on these topics and a full list of sources, click here.
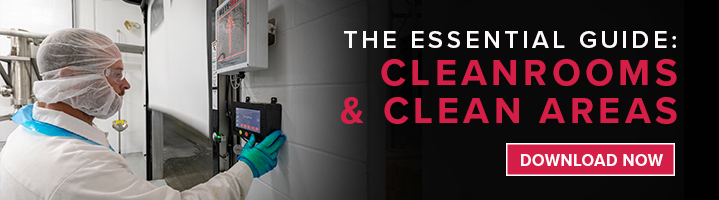