- Home
- News
- Heavy Manufacturing: 7 Must-Know Safety Regulations
Heavy Manufacturing: 7 Must-Know Safety Regulations
The dangers of heavy manufacturing machines must not be overlooked, as they can lead to serious injuries, or even death, if they aren’t properly used. To substantially reduce the risks involved with heavy manufacturing machines, industrial facility managers must thoroughly evaluate and fully apply the various regulations that have been implemented by OSHA, ISO and RIA, along with the standards that have been developed by their national government.
Understanding the risks and hazards associated with industrial robots and heavy duty material handling equipment, managers and workers can be better prepared for the future of loading docks, automation and supply chains.
Here are 7 heavy manufacturing regulations facility and safety managers should have their eyes on at all times:
OSHA 29 CFR 1910.212(a)(3)(ii): General Requirements for All Machines (U.S.)
This standard states that every machine should be guarded if its operation exposes employees to injury. Any type of guarding device should be designed and constructed in a manner that prevents operators from having any part of their bodies in danger zones throughout the operating cycle. When coupled with safety interlocks, automated barrier doors not only restrict access to the process, they also contain secondary hazards such as smoke, flash, splash, mist or flying debris associated with automated welding operations by placing a barrier between machine operators and machine movement. These types of guards are an ideal alternative to light curtains and other presence-sensing devices in many situations.
ISO 13849-1: Safety-Related Parts (INTERNATIONAL)
As it relates to the safety of machinery, this regulation begins with a risk estimation, as well as a risk reduction process: Determine the limits of the machinery, identify hazards, estimate risk, evaluate risk, determine if the risk is acceptable and then re-evaluate with new solutions.
While machines automate operations that were formally manual (not to mention potentially dangerous to begin with), they can also create their own category of risk and danger, which should ultimately be guarded when possible.
ISO 13857: Safety Distances (INTERNATIONAL – UNDER REVIEW)
This standard focuses on preventing injuries to limbs, as workers interface with potentially dangerous machines or operations, by using a distance formula. Through this formula, appropriate values for safety distances in industrial, as well as non-industrial, environments can be determined. In doing so, the odds of machinery hazard zones being reached will decrease considerably. Automated barrier doors offer a solution, as they create a physical barrier that workers cannot easily bypass.
ISO 10218-1&2: Robot Safety (INTERNATIONAL)
The requirements and guidelines for the inherent safe design of industrial robots, along with protective measures and information for the usage of them, is covered in these related standards. Moreover, it describes basic hazards and provides ways to eliminate or adequately reduce such hazards.
However, the regulation doesn’t address robots as complete machines, nor it doesn’t apply to non-industrial robots. Even so, the safety principles established in ISO 10218 can still be utilized for these other types of robots. To help mitigate the hazards associated with industrial robots, workers should avoid directly interacting with them while they’re in operation, particularly through the usage of physical work cells, which are protected with fixed and automated barriers.
RIA 15.06-15: Risk Assessment (NORTH AMERICAN)
While OSHA regulations tend to be broad, industry-specific regulations like RIA 15.06-15 get much more specific. Adopting ISO 10218-1&2, this RIA standard places extra emphasis on risk assessments and harmonizes global standards that control the safety rated motion of robots. Once risk assessments are performed though, the distinct advantages that automated barrier doors, as well as fixed barrier systems around work cells provide, are obvious.
CAN/CSA Z434: Risk Assessment (CANADIAN)
Like OSHA, many Canadian regulations are very broad and reference specific regulations like CAN/CSA Z434, which was written in accordance with RIA R15.06. This was intentional. This Canadian regulation corresponds with the same expectations laid out in the internationally recognized RIA standard. This regulation also places extra emphasis on risk assessments and harmonizes global standards, which control the safety rated motion of robots.
JAS/ANZ AS/NZS ISO 9001: Quality Management Systems (INTERNATIONAL/AUSTRALIAN/NEW ZEALAND)
The 2015 update to ISO 9001 actually places a stronger emphasis on risk-based thinking, which includes “customers seeking confidence in an organization’s ability to consistently provide products and services conforming to their requirements.” Furthermore, risk-based thinking also includes “organizations seeking confidence in their supply chain that their product and service requirements will be met.”
This particular regulation doesn’t specifically refer to RIA 15.06 as it is much more wide-ranging in the types of applications it covers, but it places a strong emphasis on completing a risk assessment. After completing a risk assessment to determine whether or not their product and service requirements will be met, facilities should consider state-of-the-art solutions at the loading dock, as well as inside the plant, which will improve supply chain integrity.
General Rule of Safety
When in doubt, err on the side of safety. Regulations are being updated constantly in an effort to keep up with new technology and new processes. If your facility is implementing new robots or processes, conduct a risk assessment and consider ways to protect workers before an accident happens.
This blog was developed from the Essential Guide: Safety Regulations. For additional information on these topics and a full list of sources, click here.
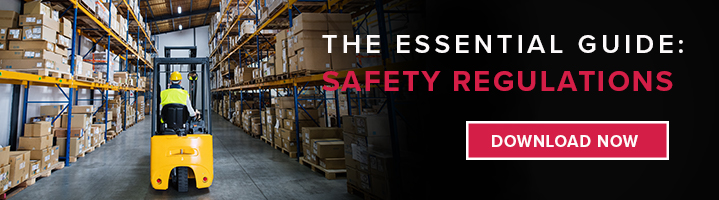