- Home
- News
- Trends in Cleanrooms and Clean Areas: Food and Pharmaceutical
Trends in Cleanrooms and Clean Areas: Food and Pharmaceutical
Perhaps more than ever, product integrity and contamination control are ever-present concerns in any industry. Long before our recent pandemic, cleanrooms and wash-down protocols can play a key role in ensuring both. Removing contaminants from production processes is imperative to meet standards and provide the highest quality products.
Cleanrooms and clean areas are most ubiquitous in the food and pharmaceutical industries. Let’s look at how cleanrooms and clean areas help to remove airborne particles, vapors and fibers, chemicals and bacteria, in accordance with ISO regulations and/or the U.S. Food & Drug Administration (FDA).
Food Sector Trends
The importance of clean areas in the food industry is being driven by food processing technology developments, regulatory changes, and recently, global events related to COVID-19.
The explosive growth of the ready-to-eat (RTE) food category, is a major factor, as well. RTE includes an ever-widening array of precooked meats that require refrigeration, as well as cheeses, canned goods, bakery and shelf-stable fare. According to Refrigerated & Frozen Foods magazine, the global RTE food products market is expected to expand at a compound annual growth rate (CAGR) of more than 7% from 2016 to 2026, reaching an estimated valuation of nearly $200 billion at that time.
The growth of RTE foods has impacted clean areas and facility sanitation, particularly in regard to meats, seafood and animal products. If there is a breakdown in clean protocols or cold chain integrity, these products will be directly affected.
The proliferation of RTE products has also meant increasing separation of process spaces in processing facilities, keeping raw products away from cooked products. In fact, the Sanitary Transportation section of the FDA’s Food Safety Modernization Act (FSMA) stipulates that RTE foods must be prevented from touching raw food. This separation should take place both in processing and shipping areas.
Food processors across the country are stepping up their games to separate work areas like never before. Efforts to minimize the transfer of airborne bacteria are stronger than ever. Below is a sample four-step cleaning program for RTE areas:
- Rinsing with water and chlorinated alkaline cleaner (soap)
- Scrubbing with green pads or scratch pads for tough areas
- Final rinsing and pre-op (inspection of the line by sanitation team leaders and its in-house USDA inspector)
- Sanitizing with Quat sanitizer to reach the OSHA regulation of 200 parts per million
The ongoing implementation of FSMA has also increased use of cleanrooms and clean areas. The FSMA Final Rule for Preventive Controls for Human Food requires food facilities to have a food safety plan in place that includes an analysis of hazards and risk-based preventive controls to minimize or prevent identified hazards.
This rule stipulates that a food safety plan takes into account “procedures, practices and processes to ensure that the facility is maintained in a sanitary condition to minimize or prevent hazards,” such as environmental pathogens, hazards from employees handling food, and food allergens. The food safety plan must also include oversight and management of preventive controls, including monitoring, verification and corrective actions (which must be documented.)
In conjunction with the growth of organic foods, FSMA has also spurred another trend: The use of sanitizers that are alternatives to chlorine and Quat. This includes peroxyacetic acid (PAA), which is gaining acceptance for clean-in-place applications.
Pharma Sector Trends
Clean technology growth has been particularly strong in pharmaceutical manufacturing and related sectors such as biotechnology, medical device, hospitals and diagnostic centers. In fact, the global cleanroom market for these industries is now more than $3 billion (USD) with pharma accounting for nearly half. It is expected to grow at a robust CAGR of 5% through 2025.
In all industries, cleanrooms use high-efficiency particulate air (HEPA) filters to remove particles larger than 0.5 μm (0.02 mils). The goal in most cases is to maintain an air pressure differential between rooms, pushing air from the opening’s cleaner side to the less-clean side. Occasionally, the opposite approach is required and particulates must be kept within a certain room to avoid cross-contamination with the processes in adjoining rooms. For these reasons, most facilities incorporate multiple pressure steps within the building’s structure. The steps typically range from 5 to 13 Pa (0.02 to 0.05 w.g.) between rooms, but can be has as high as 50 Pa (0.2 w.g.).
Every cleanroom has a controlled level of contamination determined by the number of particles per cubic meter at a specified particle size. While regulatory bodies vary by country, the ISO (International Organization for Standardization) standards are universally recognized, with the most pertinent being ISO 14644 and its related sub-standards, as well as US FDA and cGMP requirements.
Requirements differ by application and defined by ISO classes; pharma industry cleanrooms are generally in the range of ISO 5, 6, 7 or 8. To give perspective, the outside air in a typical city contains 35 million particles per cubic meter in the range of 0.5 μm (0.02 mils) and larger in diameter, corresponding to an ISO 9 cleanroom. On the opposite end of the spectrum, an ISO 1 cleanroom allows no particles in that size range and only 12 particles per cubic meter of 0.3 μm (0.01 mils) and smaller.
In recent years, modular cleanroom construction has become more common in the pharmaceutical industry. One of the main benefits of modular construction is similar to that of high speed doors and walls for clean applications – prevention of microbial growth.
Modular cleanrooms share other benefits with fabric curtain walls as well, including their flexibility, quick installation and cost-efficiency. Modular cleanrooms can be altered and right-sized as the needs of a company change, while reusing the modular components and making use of the existing HVAC and ventilation systems, rather than requiring separate systems.
Cost concerns are also behind another developing trend – a shift toward local control zones. These local control zones present a possible future of pharmaceutical cleanrooms. These control zones will need to comply with strict standards, but the larger spaces they’re contained within don’t need to meet those standards. This can help lower operational cost.
This blog was developed from the Essential Guide: Cleanrooms and Clean Areas. For additional information on these topics and a full list of sources, click here.
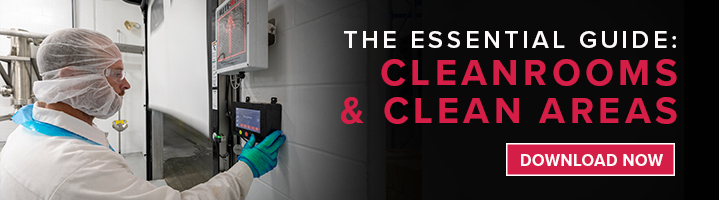